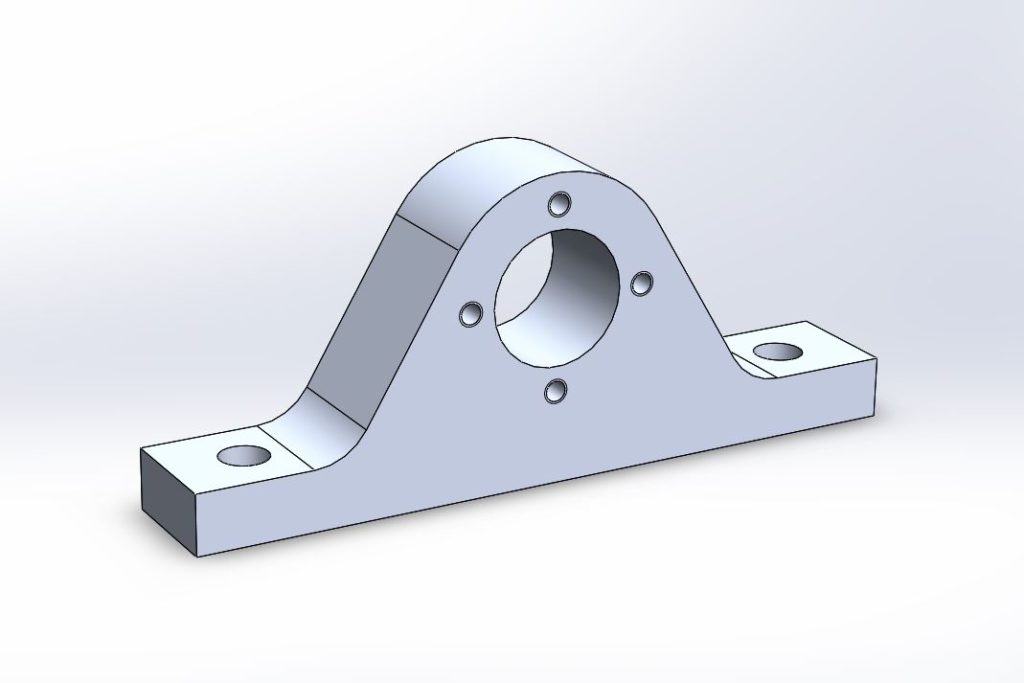
作者近日在进行机械设计过程中偶然遇到此实例,并认为其是对理解“以便于加工原则指导设计”的不可多得的典型范例,有着鲜明的教育意义,故作此文,与同业人士分享学习之。读者若对本文观点有不同见解,欢迎评论探讨,并由于作者水平有限,本文疏漏错误,还望读者不吝斧正为是。
作者此次要设计的部件是一个轴承座,轴承座的内孔装配有法兰铜套自润滑(含镶嵌石墨)滑动推力轴承。考虑到与周围零件的位置关系,装配上的需要,和美观性的要求,将该零件的外形设计为如图1所示的形状。该工件为单件生产,由于车间不具备铸造条件,加之成本问题,加工方案定为坯料直接机加工成型。
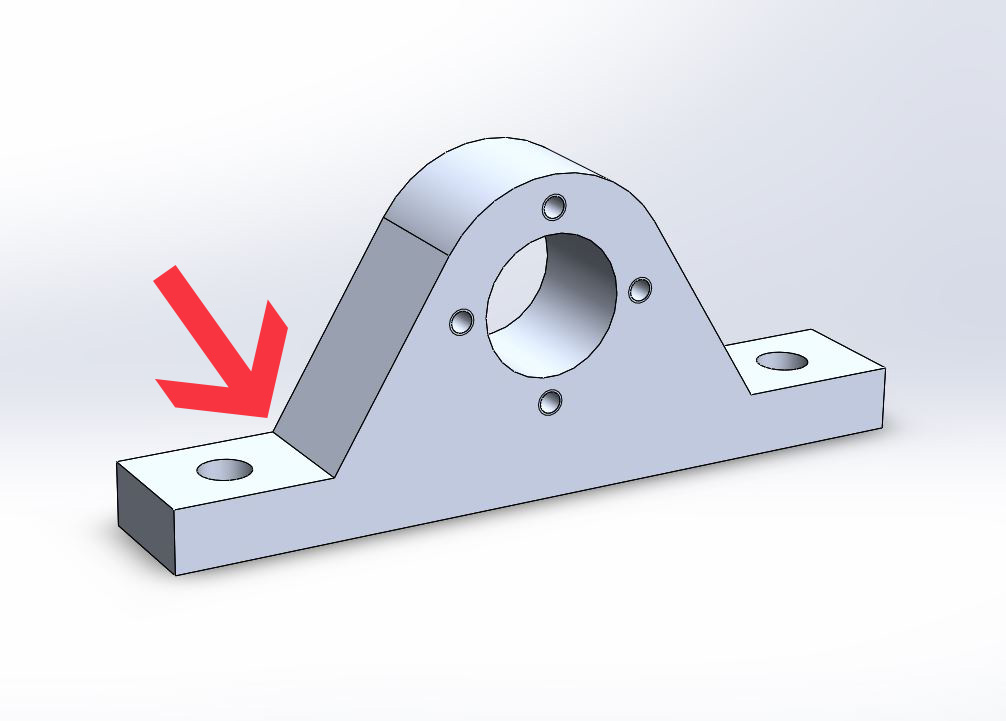
后经再三思索,作者决定在箭头所示处加入10mm圆角。加入这两个圆角,正是出于便于加工的考虑。一般而言,工件上倒圆角会增大工作量,无法便于加工,那么为什么这两个圆角能方便加工呢?本文将分析原因。
以传统的机械加工方法,无法在内凹曲线上切削尖角。以通用立式钻铣床为例,立式钻铣床使用旋转的铣刀切削工件,所以在所经过的轮廓上,即使进给突然换向,也会至少留下一个刀具半径大小的圆角,而且不论是手工铣削或是数控铣削均不能避免。因此要形成如图1所示的尖角,要么想办法去掉圆角,要么使用特种加工工艺。作者认为,如要形成尖角,可有以下办法:
- 钳工手工去掉圆角,或者使用往复运动的切削机械(如刨床)等去掉圆角。
- 坯料电火花走线切割。
- 坯料激光,等离子,或高压水刀切割。
方法1很明显要在数控铣削基础上多加一道工序(本工件的外形不适合手工铣削),从而增加了成本,不符合一般设计要求。如果让钳工手工去圆角,还不易保证加工精度,并且如果为了减小钳工工作量而减小圆角尺寸,则势必在铣削时使用小直径的刀具,降低了刚度,会损害到其他部分的精度。如果使用机械去掉圆角,不但不易达到高精度,还会产生大量的工装问题,这在单件生产中影响尤其严重。
方法2是特种加工工艺,须在有条件的车间进行,且加工成本较高。并且轴承安装孔必须在铣床上加工,产生了定心的麻烦。反观改进后的方案,一次装夹工件就可以铣出轮廓,并加工轴承孔,如果使用绝对坐标进行加工,能够得到很高的精度。
方法3的设备,尤其是能够切割25mm厚坯料的设备,不易找到,虽然加工成本比方法2低,但只有在大规模生产中才有优势。并且这些方法加工出的表面精度非常差,且一般带有斜度,需要进一步机加工以达到设计要求,而这些切割方法的加工余量又不易控制。方法3同样会产生二次铣孔时定心的麻烦。
纵观这些加工方案,不难发现,加入这两个圆角,可以使工件的加工在数控铣床上一步完成,对便于加工大有裨益。那么,为什么要选择10mm的圆角呢?这就要引入一些对于加工速度和精度的考虑。做过铣工的人都知道,铣刀的直径越大,刚度就越好,在同样的吃刀量下,形变较小,加工精度较高。所以,圆角半径越大,越能允许使用大直径的刀具进行加工,有利于保证加工精度,而10mm正是本工件上不影响螺栓头部的情况下可以容纳的最大圆角。并且,加入大圆角还有利于减小应力集中,提高工件疲劳寿命。