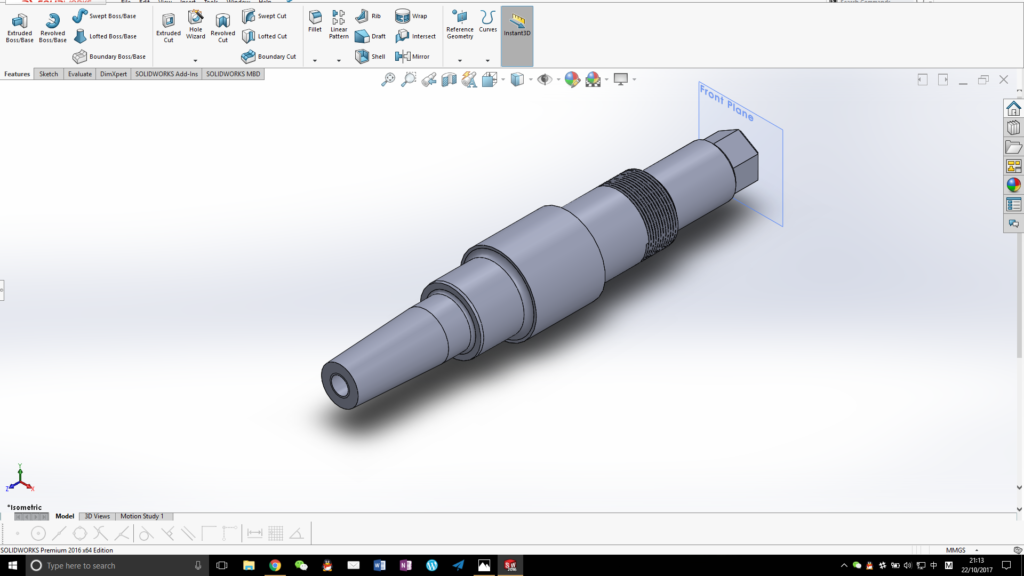
在3D建模中,完成同一零件的建模一般都有很多种方法,比如一个轴类零件的建模,就有拉伸,拉伸切除,旋转,等等方法。不同的设计人员有不同的建模习惯,而在同一零件中,不同的建模方法虽然能够达到相同的几何形状,却会形成截然不同的模型结构,这表现为设计树的巨大差异。不同的设计树结构在查看,修改,交互等方面都有明显的优劣之分,而孰优孰劣又取决于模型本身和模型用途,并没有放之四海而皆准的金科玉律。工程规模越大,要求设计人员对建模思路的掌握和践行就越加明确,严格,和一致。
因此,要求设计人员熟练掌握多种建模思路。本文介绍一种以机械加工顺序指导建模的思路,以在SOLIDWORKS中建立一个轴类零件的模型为例。3D建模软件的使用方法大同小异,因此本文所介绍的思路也可以应用于其他软件。然而值得注意的是,以加工顺序指导建模在许多情况下并不是最优方案,甚至比其他的思路要繁琐。但是,这种思考方式有助于设计者理清加工思路,便于编制技术要求,同时这样产生的模型与CNC机床的兼容性也比较好。
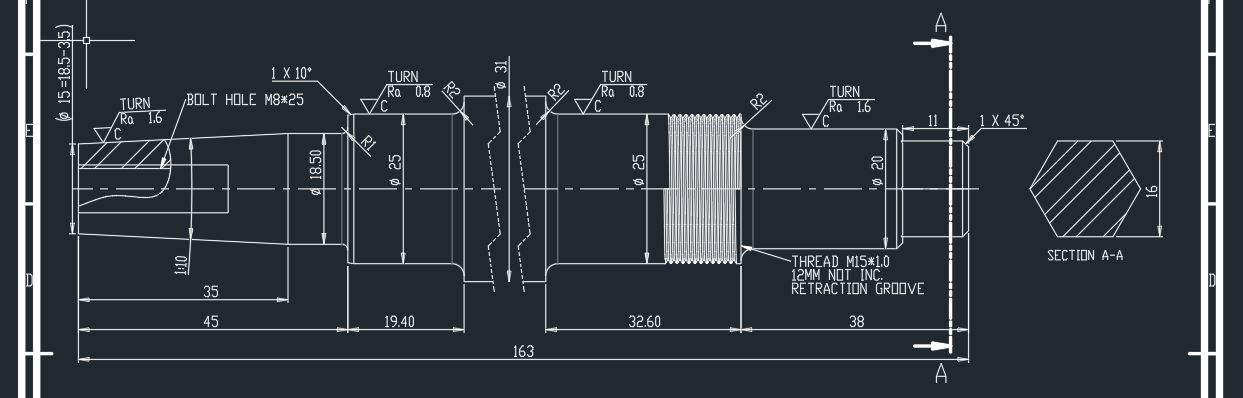
本次作者要设计的轴如图1所示,是一个阶梯轴,由两个轴承支承。一端是锥面并带有螺孔,另一端的头部要求铣成六边形。轴的一个阶梯末端需要加工一定长度的螺纹。
我们可以简单分析以下这个轴类零件的加工思路。此轴尺寸公差要求为IT7级,故主要工艺选定为车制(轴承配合面可能需要少许磨削和抛光)。螺纹为了加工方便,应选用单点仿形刀具车制,螺纹孔可以在车床上钻出并使用机用丝锥攻丝(也可以全都加工好后手工攻丝,取决于钳工水平)。轴端的六边形无法车制,需要在铣床上铣制,这可以是最后一道工序。
所以我们可以将此轴的加工工艺按时间顺序简要列举为:
- 下料
- 车端面,钻中心孔
- 粗车,精车外圆(形成轴最粗部分的直径)
- 粗车,精车左侧台阶并一并车制圆角
- 试配合轴承,并按需做少许手工抛光
- 车锥面,钻孔,攻丝,至此左侧加工完成
- 工件翻面,车制台阶并一并车制圆角
- 车螺纹
- 试配合轴承,并按需做少许抛光,至此右侧车制完成
- 在铣床分度头上装夹,铣削六角
应当指出,这并不能代表实际的操作步骤。有些车工喜欢全部先车粗再车精,而有些为了直线度和同轴度的控制需要,喜欢先车完一侧再车另一侧,有些人喜欢先抛光,有些人喜欢后抛光,本文无意讨论这些机加工的技术问题,这些顺序对我们将要进行的建模也没有影响。
现在,我们按顺序进行建模操作。首先观察前三步,我们发现这可以在SOLIDWORKS中一步完成,这是因为建模时无需体现车削端面的步骤,通常也无须体现中心孔(本工件中的中心孔有一个会在后面被钻成螺纹孔,如果画出中心孔,反倒会在后面的绘制中产生一些错误)。建模的优选方法是拉伸一个圆柱基体,在绘制草图时直接赋予本轴最粗部分的直径(31),在拉伸时直接赋予总长(163),这样就完成了步骤1,2,3。
下面的操作需要选一侧开始,我们根据阅读习惯选择从左侧开始。第一个台阶的车削,要求将从端面开始的64.4长度的直径车到25,并同时车制一个半径为2的圆角。我们首先使用拉伸切除命令,在基体的左侧绘制一个直径25的圆草图,并执行反向拉伸切除,深度64.4。完成后,再使用圆角命令加2的圆角。
仔细阅读图纸,会发现此处要求了一个1*10的倒角,这是为了方便装配轴承。不论是在加工中还是在建模中,这个倒角都只能在下一个台阶车完后才能生成。
第二个台阶的车削,要求将从端面开始的45长度的直径车到18.5,并同时车制一个半径为1的圆角。我们首先使用拉伸切除命令,在基体的左侧绘制一个直径18.5的圆草图,并执行反向拉伸切除,深度45。完成后,再使用圆角命令加1的圆角。
这时我们可以加入1*10的倒角,直接使用倒角命令就可以了,需要注意10度的方向到底是朝哪一边。
车好第二个台阶后,可以执行锥面的加工。在建模中,我们应当模拟出去除材料的加工方法,所以使用倒角的方法进行生成。没有使用本文介绍的思路的设计人员可能会选择使用拔模,或者是旋转的方法进行生成。应当注意,此处的倒角角度可以使用SOLIDWORKS自带函数命令atn( 0.05 ) rad进行生成(注意标注单位),而不是手工计算后输入,这样可以保证内部运算的准确性。
最左侧的螺纹孔,可以直接使用SOLIDWORKS的异形孔向导进行生成,注意在更改螺纹攻丝长度后可以设定自动计算钻孔深度(这个深度在实际设计和加工中影响不大,车工如果使用手工控制钻孔,为了保险起见可能钻得深一点)。至此我们完成了左侧的建模。
右侧第一个台阶的车削,要求将从端面开始的70.6长度的直径车到25,并同时车制一个半径为2的圆角。我们首先使用拉伸切除命令,在基体的右侧绘制一个直径25的圆草图,并执行反向拉伸切除,深度70.6。完成后,再使用圆角命令加2的圆角。注意到在能够熟练使用软件的情况下,这种非常简单的草图操作可以直接在3D环境下进行,减少了不必要的切换视角操作。
注意到此台阶的末端有螺纹。这个螺纹可以在SOLIDWORKS中现在加入,但实际加工中一般是车好下一个台阶后才车螺纹,所以我们暂时不加入螺纹。第二个台阶的车削,要求将从端面开始的38长度的直径车到20,并同时车制一个半径为2的圆角。我们首先使用拉伸切除命令,在基体的右侧绘制一个直径20的圆草图,并执行反向拉伸切除,深度38。完成后,再使用圆角命令加2的圆角。这都是相当重复的操作,故在此不做演示。
车好这个台阶后可以加入螺纹。其实在这个模型中,螺纹可有可无,只要最后出图时候画上螺纹就行了,但是为了方便观察,我们可以使用软件绘制出仿真的螺纹。注意此处为了达到比较好的切入视觉效果,螺纹的切入点进行了一些偏置,并且选择了“保持螺纹长度”的选项,故无需对长度做出补偿。图样中的螺纹标记有错误,M15应当为M25,并且由于M25*1.0并不是标准螺纹,需要对螺纹的直径和螺距进行超控。
至此轴件的车制就完成了,还剩下一个铣削(绘制)六角的操作,我们可以很方便地使用拉伸切除来进行,这是对铣削一个很好的模拟。值得注意的是,图样中在六角附近加入了一些倒角,而且有一个并未标明尺寸,对于这种不清晰的指示,我们在建模中可以选用差不多的尺寸。在实际加工中,这两个倒角对于实际零件功能影响甚微,应该主要是出于防止尖锐边缘伤人的考虑,故使用锉刀进行一些倒角既可。
有些读者可能有疑问,这个六角外接圆的直径比这段轴伸的直径要小,为什么不用先车到相应的直径呢?这个操作其实是完全多余的。铣削这个六边形是非常基础的手工工作,铣工在这个过程中会寻找工件的边缘并进行坐标回零,而这里正是距离中心一个半径的距离。六边形的每个面离中心的距离是8毫米,这个距离是非常容易确定的,并不需要任何有关外接圆尺寸的信息。一旦装定了这个距离,便在整个操作中无需再次调整。
我们至此完成了整个工件的建模。接下来就可以进行相应的收尾工作,如定义材料等,本文不再赘述。