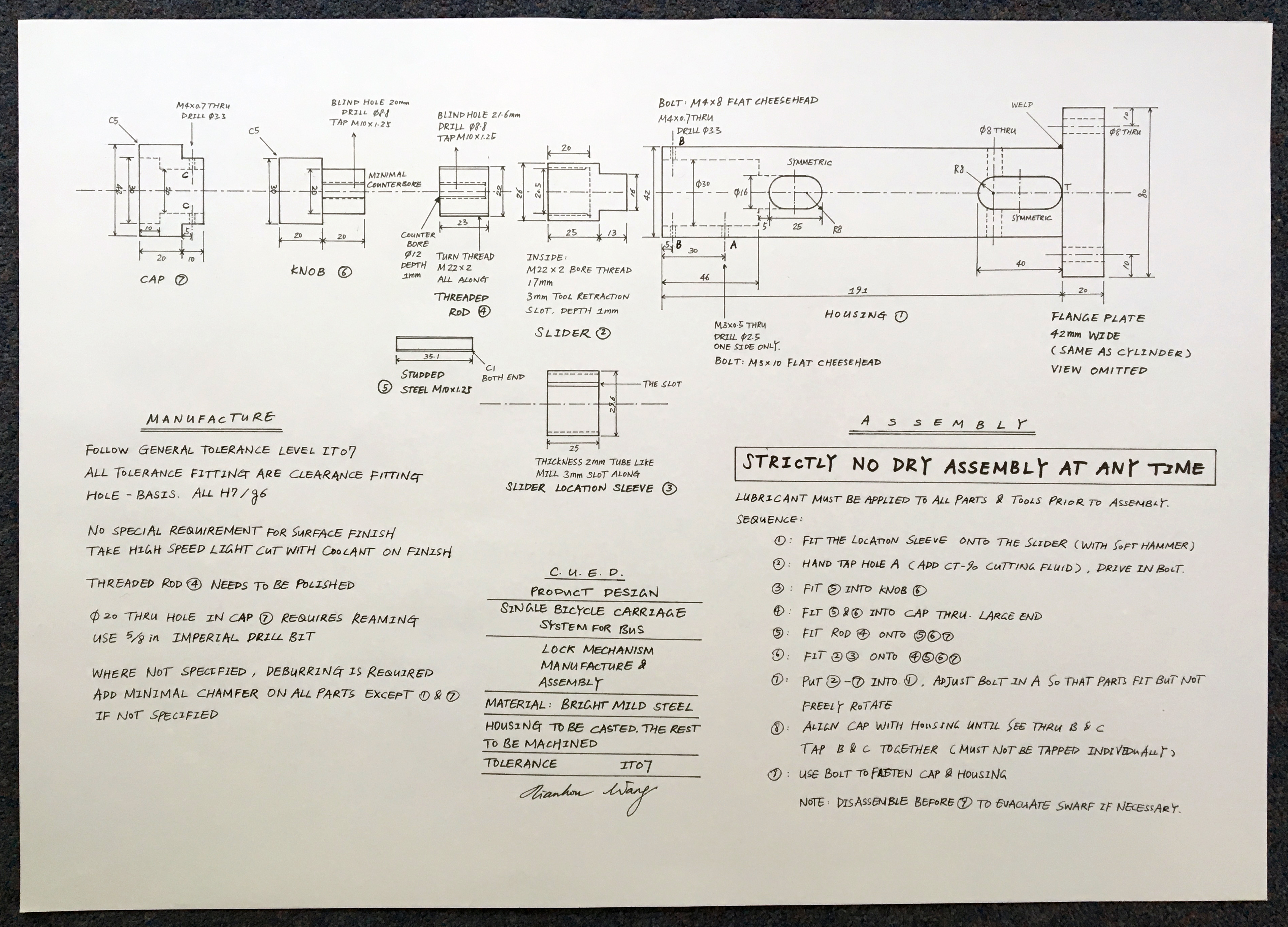
Recently I have been working on the design and prototyping of a Single Bicycle Carriage System for Bus, the design of which is to be submitted as a product design coursework I have been assigned. The prototyping of the core component, which took over three weeks, however, is not required and I did that purely out of personal interest and a desire to learn more about practical mechanical design and manufacture. This new series of articles is to record the process by which the prototype was made and to summarise the highlights and errors in this effort.
The designed product is a lightweight, compact, rapidly deployed-on-demand system for a bus to carry one bicycle. Similar products have been in the market for some time, but those now available all have the capability to carry several bicycles, resulting inevitably that they are bulky, impairing the ability of the bus to manoeuvre, stays in the same place whether being used or not, and expensive. Therefore, this product is to offer an affordable solution to the very occasional need for a bus to carry one bicycle (for example, to rescue cyclists who might be injured or suffering from a punch).
The biggest highlight of this system is that it is to be designed so that most of it can be detached from the bus when not in use, and able to be rapidly deployed by the passenger himself/herself. The system ought to be safe, easy to use, and passenger friendly (i. e. not producing noise, resulting in the bus to be untidy, or damaging the bicycle). The basic idea is to hang a bicycle at the rear of the bus horizontally on its wheels with two locked hooks, each mounted onto a slider which can slide into or out of the rail (permanently attached) and freely positioned. The system is to be made out of strong aluminium alloy with a wide application of casting, welding, and sheet metal forming, while demanding for minimal machining which is expensive.
It is critical whether the hook and lock system can be made to be secure and lightweight, as this a matter of health and safety. Therefore, the possibility of this has been investigated in detail, resulting in the first version of mechanical design to be made, and a prototype fabricated to validate the design. The main aim of the prototype is to validate the design and prove it to be functional, and also to test whether the design has a certain tolerance to inaccurate geometries (a common feature of casting), lack of lubrication, and mishandling (which is to be expected for a passenger operated system).
The idea of the hook and lock system is taken from a conventional D lock for bicycles. However, instead of operated by keys, this mechanism is to be operated by special tools (in order to prevent unauthorised access). The prototype uses a knob to substitute that. Bright mild steel was also used instead of aluminium alloy, in which I had no option give the limited stock of the department material store. The driving mechanism for the lock is conventional thread transmission.
In the following articles, I will focus on documenting the prototyping process, and I plan to spend about 10 articles to do that. I hope you will enjoy these posts, and please feel free to comment and discuss with me about it if you are interested.
Many thanks to Mr Andy Last, technician of Dyson Centre for Engineering Design, who acted as my mentor in making the prototype (and also trained me to use machine tools beforehand).